It’s rare to see items labeled “Made in USA”—but several indispensable products are made right here in Colorado. A rarified subset of these even have ingredients that come from in-state, rather than being assembled here using parts manufactured in far-flung places. One of them surrounds you—drywall.
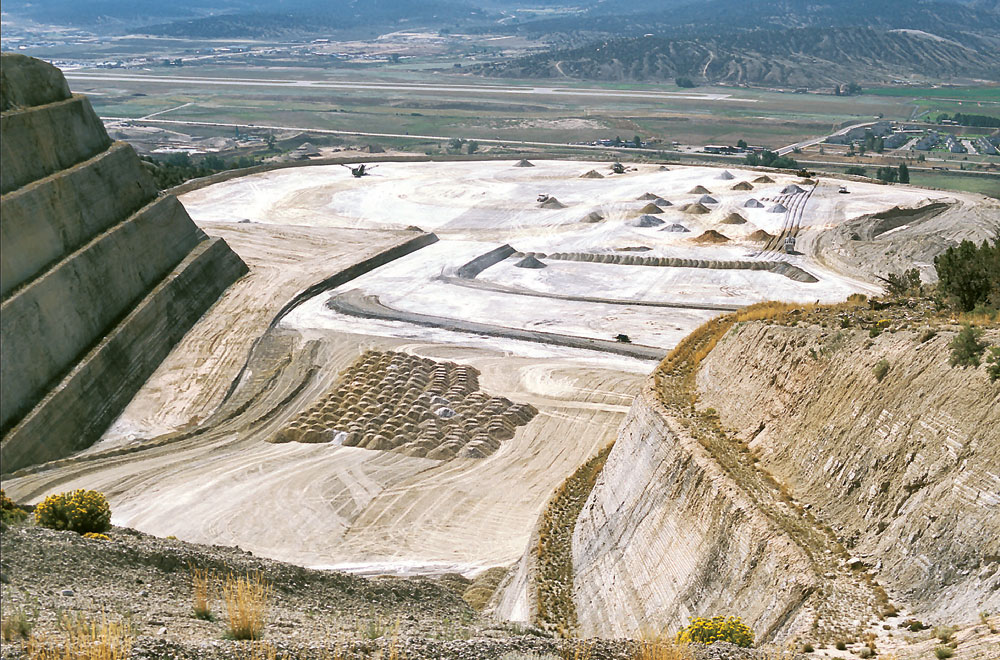
Looking southward from the top of one of the main gypsum quarries in Gypsum, CO. Foreground: Crushed gypsum and waste rock piled in the quarry floor; in the distance is the Eagle-Gypsum airport. Photo: American Gypsum
Sometimes known as gyp-board or sheet-rock, this inconspicuous product lines the walls of most homes and businesses. Back in the day, walls were made of lath-and-plaster, but such material fell out of favor because it was heavy, less fire resistant, and hard to patch. Not to mention that it took a week to plaster a home versus two days to hang and mud drywall. As a result, most builders use drywall to mantle a building’s interior framing.
The key ingredient in drywall is a type of salt called gypsum (CaSO4 2H20). It’s known to mineral collectors as selenite or desert roses, to sculptors as alabaster, and to kids everywhere as “plaster of Paris.” Gypsum has some unusual structural properties that make it like Mother Nature’s reusable glue, mainly owing to the fact that if you heat gypsum, it easily bonds and unbonds to water (the H2O, above) and cures to a solid state.
Colorado’s gypsum occurs underground, in layered sedimentary rocks that were originally deposited on the seafloor 250–300 million years ago, when Colorado was an ancient sea. Like rock candy that grows on a string as sugar-saturated water cools, our gypsum grew on the seafloor as the salty waters of the ocean evaporated, and its water was unable to hold the salt in solution. You can witness the same process happening today, where bathtub rings of gypsum are precipitating on shorelines of the Great Salt Lake and Dead Sea.
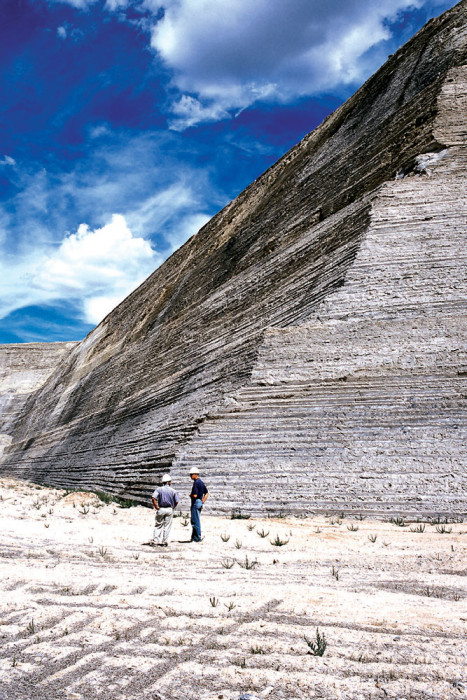
Miners discuss the stair-step-shaped wall of excavated gypsum in Gypsum, CO. Photo: American Gypsum
Gypsum has been mined here for over a century. Colorado’s smallest gypsum mines are in the Livermore area, where deposits of gypsum are so fine in their crystal structure and color that they are exported all over the country. Marketed as alabaster, artists carve Livermore gypsum into sculptures, bowls, and other ornamental art. The rest of the Livermore area’s gypsum is recycled in-state. Ground-up chunks of it are added to cement (mostly in Lyons, Colo.), where it helps stabilize the cement mix and prevents flash setup of concrete when it is mixed to line wells, make sidewalks, and poured on streets and home foundations. Finely powdered gypsum from Livermore is shipped to the San Luis and Grand valleys where potato, grape, and peach farmers use it as a soil amendment. The calcium, or “Ca” in the gypsum helps these plants avoid fungal diseases, facilitates leaching of some of the sodium in soils that inhibits plant growth, and is also taken up directly by the plants as a nutrient.
The majority of our gypsum is mined north of the Gypsum exit on I-70. There, a giant Zamboni-like machine scrapes nearly pure gypsum, layer-by-layer from the mountain. It is trucked to a football-field-sized plant south of the highway where it’s powdered, baked, and mixed in a gizmo that looks something like a giant cake-mixer. The gypsum-water mix is then squeezed out between two giant rolls of recycled paper (hailing from Oklahoma City), where it’s squeezed, dried, and chopped into sheets like those you might see at Home Depot or Lowe’s. Take a peek next time you’re there—over 80 percent of their drywall is made in Colorado. We produce so much drywall that it’s exported by truck and by rail to many western and Midwestern states. The American Gypsum Company produces it so fast that they could pave a lane of I-70 from downtown Denver to Glenwood Springs in 24 hours. Whoa!
A multimillion-dollar business, Colorado gypsum impacts our economy, our homes, and our foods. So next time you’re chowing some Palisade peaches, mashing some Alamosa potatoes, or drinking some Petit Verdot, perhaps give a wink to this seabottom salt.
James Hagadorn, Ph.D., is a scientist at the Denver Museum of Nature & Science. Suggestions and comments are welcome at jwhagadorn@dmns.org.
0 Comments